Technology has revolutionized the manufacturing industry in countless ways, and one of the most significant advancements is the rise of mounter machines. These innovative devices have completely transformed the way products are assembled and manufactured.
In this comprehensive guide, we will delve into the world of mounter machines and explore how they have become an essential tool for manufacturers worldwide. From their evolution over the years to their intricate functions and applications, we will leave no stone unturned. Whether you’re a manufacturing professional looking to enhance your production line or simply curious about the role of technology in modern manufacturing, this guide is for you.
Discover how mounter machines have increased efficiency, lowered costs, and improved overall productivity in the manufacturing process. We will also explore the different types of mounter machines available, their features, and how they cater to various industries.
Join us as we uncover the comprehensive guide to mounter machines and witness firsthand how technology is reshaping the manufacturing landscape. Embrace the future of manufacturing and harness the power of mounter machines to stay ahead in today’s rapidly advancing world.
The role of mounter machines in manufacturing
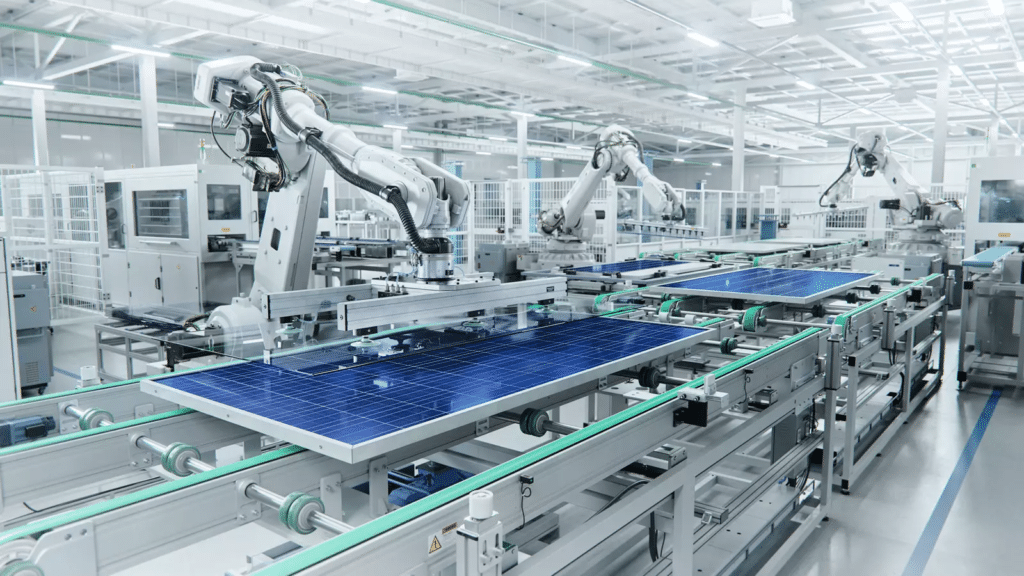
Mounter machines have become an integral part of the modern manufacturing landscape. These innovative devices play a crucial role in the efficient and precise assembly of a wide range of products, from electronic components to automotive parts. As the manufacturing industry continues to evolve, the importance of mounter machines has only grown, as they have become indispensable tools for maintaining a competitive edge in the global market.
At the heart of mounter machines lies their ability to automate the placement and assembly of components with unparalleled accuracy and speed. These machines are designed to handle a variety of tasks, including component picking, placement, and even soldering, all while ensuring consistent quality and reducing the risk of human error. By automating these labor-intensive processes, mounter machines have revolutionized the way manufacturers approach production, enabling them to increase throughput, reduce costs, and improve overall efficiency.
The versatility of mounter machines is another key factor in their widespread adoption. These machines can be customized to cater to the specific needs of different industries, from electronics and aerospace to medical device manufacturing. As the manufacturing landscape continues to diversify, the ability of mounter machines to adapt and accommodate various production requirements has made them an essential asset for companies looking to stay ahead of the curve.
Advantages of using mounter machines
One of the primary advantages of using mounter machines in manufacturing is the significant increase in productivity and efficiency. These machines are designed to operate at lightning-fast speeds, enabling manufacturers to churn out products at a much higher rate compared to manual assembly methods. This enhanced throughput not only translates to higher output but also allows companies to meet the growing demand for their products more effectively.
In addition to boosting productivity, mounter machines also contribute to improved quality control and consistency. By automating the assembly process, these machines eliminate the potential for human error, ensuring that every component is placed with pinpoint accuracy and precision. This consistency in quality is crucial for manufacturers, as it helps to reduce the risk of defects and recalls, ultimately enhancing customer satisfaction and brand reputation.
Another significant advantage of mounter machines is their ability to reduce labor costs. Automating the assembly process with these machines means that manufacturers can rely on fewer human operators, thereby lowering the overall labor costs associated with production. This cost-saving advantage is particularly valuable in industries where labor expenses can eat into profit margins, making mounter machines a strategic investment for companies looking to optimize their operations.
Types of mounter machines
Mounter machines come in a variety of types, each designed to cater to specific manufacturing needs and requirements. Understanding the different types of mounter machines is crucial for manufacturers to select the right solution for their production processes.
One of the most common types of mounter machines is the pick-and-place machine. These machines are primarily used for the automated placement of electronic components, such as resistors, capacitors, and integrated circuits, onto printed circuit boards (PCBs). Pick-and-place machines are renowned for their speed, accuracy, and versatility, making them a popular choice for high-volume electronics manufacturing.
Another type of mounter machine is the chip shooter, which is specifically designed for the high-speed placement of small, lightweight components. These machines are particularly useful in the production of smartphones, tablets, and other compact electronic devices, where the precise placement of tiny components is critical. Chip shooters are known for their lightning-fast speeds, often reaching placement rates of over 100,000 components per hour.
In addition to pick-and-place machines and chip shooters, there are also specialized mounter machines for specific industries. For example, in the automotive industry, mounter machines are used for the precise placement of components such as sensors, wiring harnesses, and even entire dashboard assemblies. These industry-specific mounter machines are designed with the unique requirements of the sector in mind, ensuring optimal performance and efficiency.
Key features to consider when choosing a mounter machine
When selecting a mounter machine for their manufacturing operations, there are several key features that manufacturers should consider to ensure they choose the right solution for their needs.
One of the most important factors is the machine’s placement speed and accuracy. Manufacturers should look for mounter machines that can handle high-volume production while maintaining exceptional precision in component placement. The faster the machine can operate and the more accurate it is, the more efficient and cost-effective the manufacturing process will be.
Another crucial feature to consider is the machine’s flexibility and adaptability. Manufacturing processes can often change and evolve, and it’s essential that the mounter machine can accommodate these changes. Manufacturers should look for machines that can handle a wide range of component sizes and shapes, as well as the ability to be easily reconfigured or reprogrammed to accommodate new production requirements.
The machine’s ease of use and maintenance is also an important consideration. Manufacturers should look for mounter machines that are user-friendly, with intuitive controls and software that simplify the setup and operation processes. Additionally, the machine should be designed for easy maintenance and servicing, reducing downtime and ensuring optimal performance over the long term.
How mounter machines are revolutionizing the manufacturing industry
The impact of mounter machines on the manufacturing industry cannot be overstated. These innovative devices have transformed the way products are assembled, leading to significant improvements in efficiency, quality, and cost-effectiveness.
One of the most significant ways in which mounter machines are revolutionizing manufacturing is through their ability to increase production speed and output. By automating the component placement and assembly processes, these machines can operate at lightning-fast speeds, allowing manufacturers to churn out products at a much higher rate than traditional manual methods. This enhanced throughput not only boosts overall productivity but also enables companies to meet the growing demand for their products more effectively.
In addition to improving production speed, mounter machines have also had a profound impact on quality control. By eliminating the potential for human error, these machines ensure consistent and precise component placement, resulting in a higher level of product quality and reliability. This, in turn, has led to a reduction in defects, recalls, and customer complaints, ultimately enhancing brand reputation and customer loyalty.
The cost-saving benefits of mounter machines have also been a significant driver of their widespread adoption in the manufacturing industry. By automating labor-intensive tasks and reducing the need for human operators, these machines have helped manufacturers lower their production costs, leading to increased profitability and a more competitive edge in the global market. This cost-saving advantage is particularly valuable in industries where labor expenses can be a significant burden on profit margins.
Case studies of successful implementation of mounter machines
To fully understand the impact of mounter machines on the manufacturing industry, it’s helpful to examine real-world case studies of companies that have successfully implemented these innovative devices.
One such example is the electronics manufacturer ABC Electronics, which faced a significant challenge in keeping up with the growing demand for its products. By investing in a state-of-the-art pick-and-place mounter machine, the company was able to dramatically increase its production capacity, enabling it to meet the market’s needs more effectively. The mounter machine’s high speed and precision allowed ABC Electronics to streamline its assembly process, leading to a 30% increase in throughput and a 15% reduction in production costs.
Another case study is that of XYZ Automotive, a leading manufacturer of automotive components. The company was struggling with the manual assembly of complex wiring harnesses, which was not only time-consuming but also prone to errors. By implementing a specialized mounter machine designed for the automotive industry, XYZ Automotive was able to automate the wiring harness assembly process, resulting in a 25% improvement in production efficiency and a 20% reduction in defects. This, in turn, led to increased customer satisfaction and a stronger competitive position in the market.
These case studies demonstrate the tangible benefits that mounter machines can bring to manufacturing operations, from increased productivity and cost savings to enhanced quality control and customer satisfaction. By embracing the power of these innovative devices, companies across various industries have been able to stay ahead of the curve and maintain a competitive edge in the rapidly evolving manufacturing landscape.
Challenges and limitations of using mounter machines
While mounter machines have undoubtedly revolutionized the manufacturing industry, there are also some challenges and limitations that manufacturers must consider when implementing these technologies.
One of the primary challenges is the upfront investment required to acquire and install a mounter machine. These specialized devices can be quite expensive, and the initial capital outlay can be a significant barrier for some companies, especially smaller or mid-sized manufacturers. Additionally, the integration of a mounter machine into an existing production line may require additional infrastructure upgrades or modifications, further increasing the overall cost of implementation.
Another challenge is the need for specialized technical expertise to operate and maintain mounter machines. These devices require skilled technicians and programmers to ensure optimal performance, troubleshoot any issues, and adapt the machines to changing production requirements. Manufacturers must be willing to invest in ongoing training and development for their workforce to ensure that they can effectively leverage the capabilities of their mounter machines.
Limitations in the flexibility and adaptability of mounter machines can also be a concern for some manufacturers. While many modern mounter machines are designed to accommodate a wide range of component sizes and shapes, there may still be instances where the machine’s capabilities are not a perfect fit for a particular production process. This can lead to the need for additional customization or the acquisition of multiple mounter machines to cater to diverse manufacturing requirements.
Future trends and advancements in mounter machine technology
As the manufacturing industry continues to evolve, the future of mounter machines looks increasingly promising, with a range of exciting advancements and trends on the horizon.
One of the most significant trends is the integration of advanced robotics and artificial intelligence (AI) into mounter machine technology. By incorporating these cutting-edge capabilities, manufacturers can expect even greater levels of speed, precision, and flexibility in their production processes. For example, AI-powered mounter machines may be able to autonomously adapt to changing production requirements, optimize component placement, and even predict and prevent potential issues before they occur.
Another trend is the increasing focus on sustainability and environmental responsibility in the manufacturing industry. As a result, mounter machine manufacturers are developing more energy-efficient and eco-friendly designs, incorporating features such as reduced power consumption, recyclable materials, and the ability to minimize waste and emissions. This shift towards greener manufacturing solutions will not only benefit the environment but also appeal to consumers and regulatory bodies that are increasingly demanding more sustainable practices.
The integration of Internet of Things (IoT) technology is also expected to play a significant role in the future of mounter machines. By connecting these devices to the broader manufacturing ecosystem, manufacturers can leverage data-driven insights to optimize production, predict maintenance needs, and enhance overall equipment effectiveness (OEE). This connectivity will enable manufacturers to make more informed decisions, reduce downtime, and maintain a competitive edge in the ever-evolving market.
Conclusion: Embracing the future of manufacturing with mounter machines
As the manufacturing industry continues to evolve, the role of mounter machines in shaping the future of production processes cannot be overstated. These innovative devices have already revolutionized the way products are assembled, leading to significant improvements in efficiency, quality, and cost-effectiveness.
By automating the component placement and assembly processes, mounter machines have enabled manufacturers to increase their production speed and output, meet growing market demands more effectively, and enhance the overall quality and reliability of their products. Additionally, the cost-saving benefits of these machines have made them an invaluable asset for companies looking to optimize their operations and maintain a competitive edge in the global marketplace.
As the technology behind mounter machines continues to advance, the future of manufacturing looks increasingly promising. From the integration of AI and robotics to the incorporation of sustainable and IoT-enabled features, the capabilities of these machines are poised to reach new heights, transforming the way we think about the manufacturing process.
By embracing the power of mounter machines, manufacturers can position themselves at the forefront of the industry, reaping the benefits of increased efficiency, improved quality, and enhanced profitability. As the manufacturing landscape continues to evolve, the companies that invest in and leverage the latest mounter machine technologies will be the ones that thrive in the years to come.